 |
Please use our services. We look forward to your comments and requests. |
|
 |

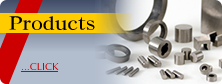

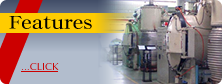

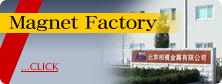

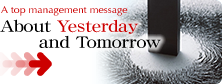

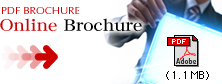

|
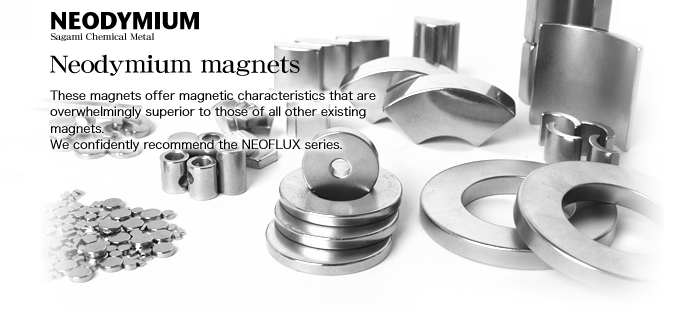


This type of magnet achieves the highest magnetic energy of all permanent magnets now in practical use. The main phase of the magnetism of rare-earth magnets developed conventionally was a two-component alloy. However, neodymium magnets combine neodymium with iron and boron to constitute a three-component, anisotropic-sintered rare-earth magnet with an atomic ratio of Nd 2 Fe 14 B 1.
The neodymium magnet exhibits excellent performance in terms of size reduction, thinning, weight reduction and enhancing the efficiency of applied equipment. However, its magnetic characteristics and corrosion-resistance performance require caution in use of the product at high temperature. For the dynamic characteristics of the product at high temperature, the Br temperature characteristics of the magnet must be sufficiently considered.
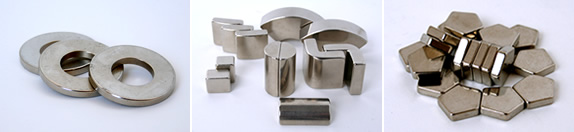
- The main characteristics of neodymium magnets are as follows:

a) |
Its maximum energy product (BH max) far exceeds that of ferrite (4.5 MGOe) and samarium-cobalt magnets (30 MGOe). Some models even exceed 48 MGOe. |
b) |
Since it consists mainly of relatively inexpensive neodymium and iron, it offers better cost performance than samarium-cobalt magnets that contain much cobalt, and poses no concern over availability. |
c) |
Although these magnets have temperature characteristics inferior to those of samarium-cobalt magnets, heat-resistant materials have been developed with higher magnetic coercive force for the following: NF-H series, NF-SH series and NF-UH series. |
d) |
Of the main components, iron accounts for nearly 70%. To ensure rustproofing, these magnets are equipped with Ni electrolytic plating as standard. |
* Caution that you should exercise
For high-temperature demagnetization, refer to the Hcj temperature characteristics of the magnets. For the NF series, we therefore provide different materials with various Hcj levels. Even with the same material, these magnets vary in demagnetization characteristics according to shape. These materials also make the magnets prone to rusting.
Therefore, the products should undergo surface treatment.
- Surface treatment
Our standard surface treatment is done by electrolytic nickel plating. We can also deliver magnets with other specifications that meet the uses of magnet users, such as gold plating, epoxy resin coating and fluororesin coating.
* Click here for the surface treatment of neodymium magnets. |




 |
Material name
|
Residual flux
density(Br)
|
Magnetic coercive force |
(BH) max |
(Hcb)
|
(Hcj) |
 |
NF-H, NF-SH, NF-UH series |
kG/T |
kOe/kA/m |
kOe/kA/m |
MGOe/kj/m3 |
 |
NF35H
|
11.8 - 12.5
1.18 - 1.25
|
≥11.0
≥875 |
≥17.0
≥1353 |
33 - 37
263 - 294 |
 |
NF38H |
12.2 - 13.0
1.22 - 1.30
|
≥11.5
≥915 |
≥17.0
≥1353 |
36 - 40
286 - 318 |
 |
NF41H
|
12.6 - 13.2
1.26 - 1.32 |
≥11.8
≥939 |
≥17.0
≥1353 |
38 - 42
302 - 334 |
 |
NF44H |
13.0 - 13.7
1.30 - 1.37 |
≥12.1
≥963 |
≥16.0
≥1274 |
41 - 45
326 - 358 |
 |
NF48H
|
13.7 - 14.3
1.37 - 1.43 |
≥12.9
≥1026 |
≥16.0
≥1274 |
45 - 49
358 - 390 |
 |
NF35SH |
11.8 - 12.5
1.18 - 1.25 |
≥11.0
≥875 |
≥20.0
≥1592 |
33 - 37
263 - 294 |
 |
NF39SH
|
12.3 - 13.0
1.23 - 1.30 |
≥11.6
≥923 |
≥20.0
≥1592 |
36 - 40
287 - 318 |
 |
NF42SH |
12.8 - 13.3
1.28 - 1.33 |
≥12.0
≥955 |
≥20.0
≥1592 |
39 - 43
310 - 342 |
 |
NF30UH
|
10.8 - 11.6
1.08 - 1.16 |
≥10.2
≥812 |
≥25.0
≥1989 |
28 - 32
223 - 255 |
 |



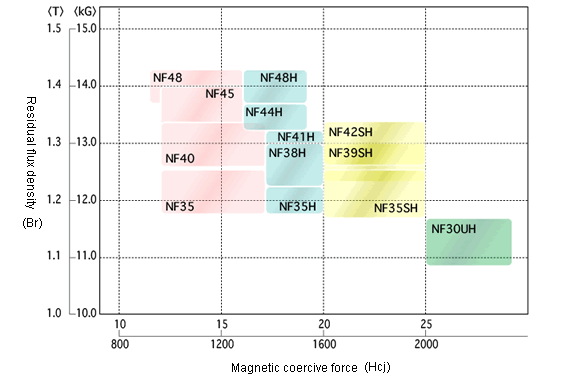



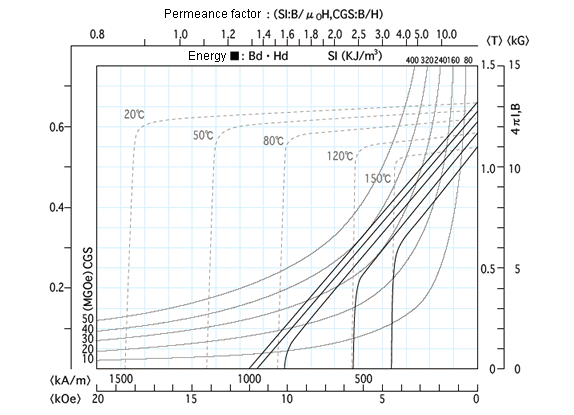


 |
|
Temperature
coefficient
(20°C - Tw) |
Density
(D) |
Curie
temperature
(Tc) |
Vickers
hardness
(HV) |
*Operating
temperature
(°C) |
 |
|
-%/°C |
g/m3 |
°C |
|
Tw |
 |
 |
 |
Series name |
αBr |
αH |
|
|
|
|
 |
NF-H series
|
0.11 |
0.6 |
7.3 - 7.5 |
320 - 340
|
500 - 600 |
<120 |
 |
NF-SH series |
0.1 |
0.6 |
7.3 - 7.5 |
340 - 400
|
500 - 600 |
< 150 |
 |
NF-UH series
|
0.09 |
0.6 |
7.3 - 7.5 |
350 - 400
|
500 - 600 |
< 180 |
 |

*Operating temperature
This is when cylinder L/D = 0.7 (Pc≒2). If the L/D level is low (small thickness), other considerations are necessary. |
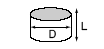 |


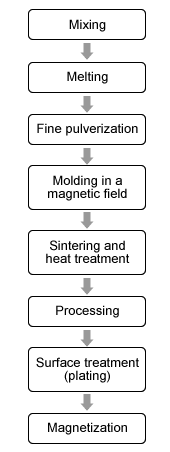 |

1. |
Mix the ingredients. |
2. |
Dissolve the mixture at high temperature and prepare an alloy. |
3. |
Turn the alloy into fine powder. |
4. |
When pressing the fine powder, apply a magnetic field to it and prepare a molded product of powder with aligned directions of magnetization. |
5. |
Sinter the product at about 1,100°C, and then subject it to heat treatment at about 600°C to increase its magnetic characteristics. |
6. |
Process the manufactured magnet base material and finish it into the product shape. |
7. |
Subject the product to surface treatment in order to make it rustproof. |
8. |
Apply a magnetic field to give the magnet magnetism. |
|
|


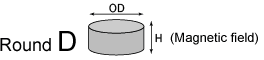 |
|
|
 |
Dimensions |
Surface flux
density |
Attraction |
 |
OD |
|
H |
GAUSS |
mT |
kg |
 |
1 |
× |
3 |
** |
** |
** |
 |
1 |
× |
5 |
** |
** |
** |
 |
2 |
× |
1 |
2200 |
220 |
0.04 |
 |
2 |
× |
2 |
2800 |
280 |
0.04 |
 |
2 |
× |
3 |
3000 |
300 |
0.05 |
 |
2 |
× |
5 |
3100 |
310 |
0.05 |
 |
3 |
× |
1.5 |
2800 |
280 |
0.10 |
 |
3 |
× |
2 |
3100 |
310 |
0.11 |
 |
3 |
× |
3 |
3500 |
350 |
0.12 |
 |
3 |
× |
4 |
3700 |
370 |
0.13 |
 |
4 |
× |
2 |
3100 |
310 |
0.20 |
 |
4 |
× |
3 |
3600 |
360 |
0.23 |
 |
4 |
× |
5 |
4000 |
400 |
0.26 |
 |
4 |
× |
10 |
4300 |
430 |
0.27 |
 |
5 |
× |
1.5 |
2500 |
250 |
0.25 |
 |
5 |
× |
2 |
2900 |
290 |
0.29 |
 |
5 |
× |
3 |
3600 |
360 |
0.35 |
 |
5 |
× |
4 |
3900 |
390 |
0.39 |
 |
5 |
× |
5 |
4100 |
410 |
0.41 |
 |
5 |
× |
6 |
4300 |
430 |
0.42 |
 |
6 |
× |
2 |
2700 |
270 |
0.39 |
 |
6 |
× |
3 |
3400 |
340 |
0.49 |
 |
6 |
× |
5 |
4100 |
410 |
0.59 |
 |
6 |
× |
6 |
4300 |
430 |
0.61 |
 |
6 |
× |
10 |
4600 |
460 |
0.66 |
 |
|
 |
 |
Dimensions |
Surface flux
density |
Attraction |
 |
OD |
|
H |
GAUSS |
mT |
kg |
 |
7 |
× |
3 |
3300 |
330 |
0.64 |
 |
8 |
× |
2 |
2300 |
230 |
0.60 |
 |
8 |
× |
3 |
3100 |
310 |
0.79 |
 |
8 |
× |
5 |
4000 |
400 |
1.0 |
 |
8 |
× |
8 |
4500 |
450 |
1.1 |
 |
8 |
× |
10 |
4700 |
470 |
1.1 |
 |
9 |
× |
3 |
2900 |
290 |
0.94 |
 |
10 |
× |
2 |
2000 |
200 |
0.80 |
 |
10 |
× |
3 |
2700 |
270 |
1.0 |
 |
10 |
× |
4 |
3300 |
330 |
1.3 |
 |
10 |
× |
5 |
3700 |
370 |
1.4 |
 |
10 |
× |
10 |
4700 |
470 |
1.8 |
 |
12 |
× |
1.5 |
1300 |
130 |
0.77 |
 |
12 |
× |
3 |
2400 |
240 |
1.3 |
 |
12.5 |
× |
2.0 |
1700 |
170 |
1.0 |
 |
14 |
× |
10 |
4400 |
440 |
3.4 |
 |
15 |
× |
1.5 |
1100 |
110 |
0.99 |
 |
15 |
× |
3 |
2000 |
200 |
1.8 |
 |
15 |
× |
5 |
3000 |
300 |
2.7 |
 |
17.5 |
× |
2.5 |
1500 |
150 |
1.8 |
 |
19 |
× |
10 |
4000 |
400 |
5.7 |
 |
22 |
× |
10 |
3700 |
370 |
7.1 |
 |
25 |
× |
6 |
2400 |
240 |
6.0 |
 |
30 |
× |
15 |
4000 |
400 |
14 |
 |
40 |
× |
10 |
2500 |
250 |
16 |
 |
50 |
× |
10 |
2100 |
210 |
21 |
 |
|
** Given its excessive measurement error, it has no value.
* The surface flux density and attraction are only for reference. |

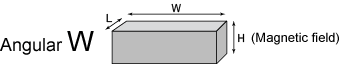 |
|
 |
Dimensions |
Surface flux density |
Attraction |
 |
W |
|
L |
|
H |
GAUSS |
mT |
kg |
 |
10 |
× |
5 |
× |
1 |
1400 |
140 |
0.36 |
 |
4 |
× |
4 |
× |
2 |
3000 |
300 |
0.25 |
 |
10 |
× |
7 |
× |
2 |
2100 |
210 |
0.76 |
 |
15 |
× |
6 |
× |
2.8 |
2700 |
270 |
1.2 |
 |
10 |
× |
3 |
× |
3 |
3300 |
330 |
0.51 |
 |
12 |
× |
7 |
× |
4 |
3300 |
330 |
1.4 |
 |
50 |
× |
20 |
× |
4 |
1500 |
150 |
7.5 |
 |
6 |
× |
6 |
× |
4.5 |
3900 |
390 |
0.72 |
 |
15 |
× |
10 |
× |
5 |
3200 |
320 |
2.4 |
 |
20 |
× |
10 |
× |
5 |
3000 |
300 |
3.0 |
 |
20 |
× |
12 |
× |
5 |
2800 |
280 |
3.4 |
 |
20 |
× |
15 |
× |
5 |
2600 |
260 |
3.9 |
 |
30 |
× |
30 |
× |
5 |
1600 |
160 |
7.4 |
 |
40 |
× |
11 |
× |
6 |
3000 |
300 |
6.6 |
 |
20 |
× |
20 |
× |
10 |
3700 |
370 |
7.4 |
 |
46 |
× |
30 |
× |
10 |
2500 |
250 |
17 |
 |
24 |
× |
24 |
× |
12.5 |
3800 |
380 |
11 |
 |
25.4 |
× |
25.4 |
× |
12.7 |
3700 |
370 |
12 |
 |
50.8 |
× |
50.8 |
× |
12.7 |
2300 |
230 |
30 |
 |
50.8 |
× |
50.8 |
× |
25.4 |
3800 |
380 |
49 |
 |
|
|

* The surface flux density and attraction are only for reference. |

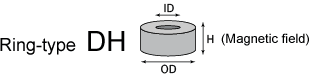 |
|
 |
Dimensions |
Surface flux density |
 |
OD |
|
ID |
|
H |
GAUSS |
mT |
 |
5.7 |
× |
3 |
× |
4 |
2900 |
290 |
 |
6.6 |
× |
2 |
× |
1.5 |
2600 |
260 |
 |
9.5 |
× |
3 |
× |
1.2 |
1800 |
180 |
 |
10 |
× |
3.2 |
× |
6 |
4300 |
430 |
 |
12 |
× |
7 |
× |
6 |
4000 |
400 |
 |
15.2 |
× |
8.8 |
× |
1.2 |
2000 |
200 |
 |
18 |
× |
7 |
× |
6 |
4100 |
410 |
 |
19.2 |
× |
15 |
× |
2 |
2700 |
270 |
 |
23 |
× |
18 |
× |
2 |
2700 |
270 |
 |
26 |
× |
20 |
× |
6 |
4100 |
410 |
 |
|
|

* The surface flux density and attraction are only for reference. |

|